By: Mike Duyck, President of Emergency Technical Decon
Firefighters face exposure to toxic contaminants every time they respond to a call. From PFAS and PAHs to heavy metals and biological hazards, dangerous substances embed themselves in turnout gear, exposing firefighters long after the fire is out.
For years, water-based washing has been the go-to method for gear cleaning, but it has serious limitations. Traditional washing fails to remove PFAS and other toxins, weakens PPE fabric and protective qualities over time, and produces hazardous wastewater. Many departments are switching to a safer, more effective alternative: Liquid CO2+ cleaning.
How Liquid CO2+ Cleaning Works
Unlike traditional washing methods, Liquid CO2+ decontamination uses a closed-loop system that removes up to 99% of specific contaminants, including PAHs, VOCs and other harmful contaminants, without damaging gear or harming the environment.
This step-by-step breakdown explains why Liquid CO2+ cleaning is superior and how it works to keep firefighter PPE safer, cleaner, and compliant with evolving regulations.
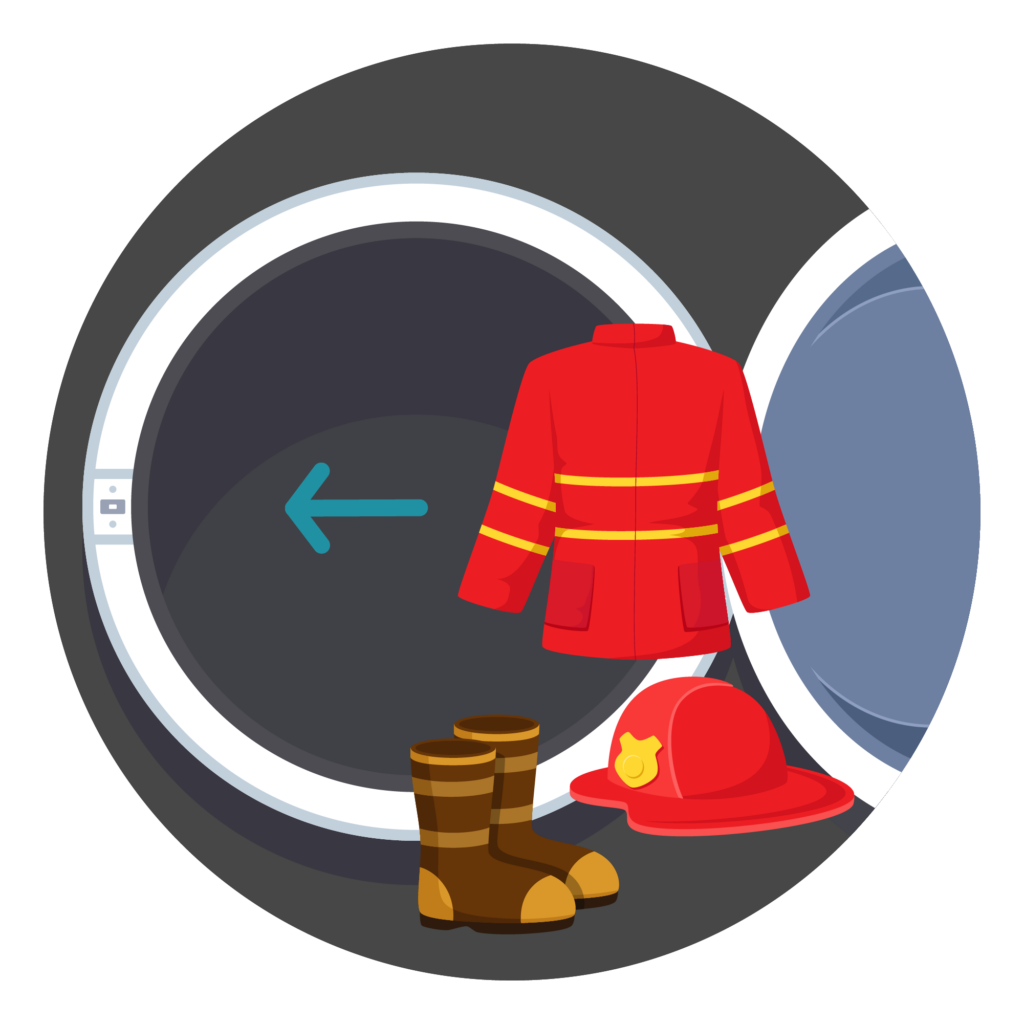
Step 1: Cycle Start – Loading Contaminated Gear
Firefighter PPE, including coats, pants, gloves, hoods, and boots, is first inspected for damage, contamination, and heavy soil levels. Once inspected, it is loaded into the Liquid CO2+ machine, such as
the ETD Enertia GFx. Unlike traditional washing machines, this system is designed specifically for turnout gear, ensuring that even the most waterproof fabrics and layers are fully penetrated.
Step 2: Pre-Wash – Initial Submersion in CoolCare™ Chemistry
Before the liquid CO2 cycle begins, the contaminated gear is submerged in an environmentally friendly CoolCare chemistry solution. This pre-wash phase loosens embedded contaminants, such as soot, hydrocarbons, and heavy metals. The machine rotates slowly to optimize cleaning, preparing the gear for the deep decontamination process.
Step 3: Drain – Filtering Out Impurities
After the pre-wash cycle, the CoolCare™ chemistry is drained from the machine and filtered for reuse. This closed-loop process ensures that harmful substances are removed from PPE without introducing them into municipal water systems.
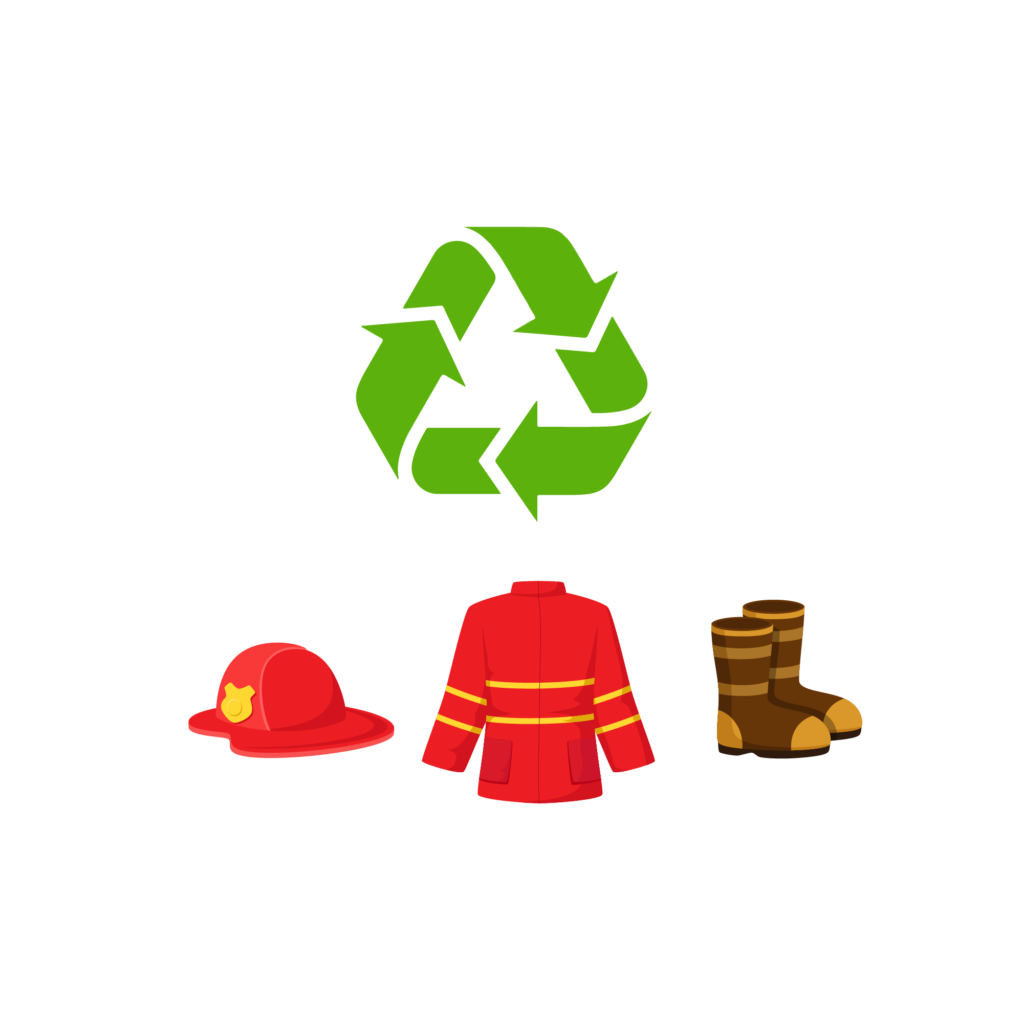
Step 4: Decon – Liquid CO2+ Rinse Cycles
Once the pre-wash solution has been drained, Liquid CO2 is injected into the chamber under controlled pressure. Multiple low-temperature liquid CO2 rinse cycles break down toxic compounds while removing targeted contaminants, including PFAS, PAHs, heavy metals, and biological hazards.
Because Liquid CO2 has a lower surface tension and viscosity than water, it penetrates deeper into fibers and removes contaminants at a microscopic level—something traditional washing simply cannot achieve. This process is also gentler on gear, ensuring moisture barriers and protective layers remain intact.
Step 5: Liquid CO2+ Drain & Recovery
After the decontamination cycle, Liquid CO2 is drained, converted back into gas, and recaptured for future cleaning cycles. This step ensures that no hazardous wastewater is produced, no contaminants are reintroduced into the environment, and fire departments remain compliant with PFAS and other toxin disposal regulations.
Unlike traditional cleaning methods that discharge contaminated water into sewage systems, Liquid CO2+ captures and isolates harmful substances for proper disposal.
Step 6: Cycle Complete – Clean, Dry, and Ready for Service
Once the cleaning process is complete, PPE is removed from the machine dry and fully decontaminated. There is no need for additional drying time, allowing gear to be returned to service immediately.
Why Liquid CO2+ Cleaning is the Future of PPE Decontamination
Now that the step-by-step process has been outlined, it’s clear why Liquid CO2+ is superior to traditional washing.
- Removes 84% of loose side chain PFAS that can be inhaled, ingested, or absorbed., while traditional washing removes only 15–40%
- Preserves gear integrity with no high heat or excessive agitation or g-force exposure
- Eliminates hazardous waste stream through a fully closed-loop system
- Reduces turnaround time, as gear comes out dry and ready for service
- Meets and exceeds NFPA 1851 and 1850 standards for PPE decontamination
- Extends gear lifespan by up to 40%, reducing long-term replacement costs
Water washing is still widely used, but it comes at a cost. High centrifugal forces, elevated temperatures (up to 120°F under the new NFPA 1850 standard), and the higher viscosity of water all contribute to breaking down gear fibers and damaging structural integrity over time. Some departments delay switching to Liquid CO2+ because gear managers report acceptable cleaning results through methods like presoaking or multiple wash cycles—but these short-term workarounds don’t eliminate the long-term damage.
And with the fire industry moving toward turnout gear with PFAS free—gear that already faces tradeoffs in strength,durability and breathabilty—the importance of gentler, more effective cleaning methods becomes even more critical. Protecting your investment in PPE means rethinking how you care for it.
At Emergency Technical Decon (ETD), we provide the fire industry’s most effective Liquid CO2+ cleaning service. Our technology, backed by Cool Clean Technologies, is proven to remove 99% of PFAS, PAHs, heavy metals, and other toxic residues while preserving the life of your PPE and eliminating environmental hazards.
Fire departments across the country are making the switch to Liquid CO2+ decontamination. Is yours? Contact ETD today to learn how Liquid CO2+ cleaning can help your department meet safety, compliance, and sustainability goals.